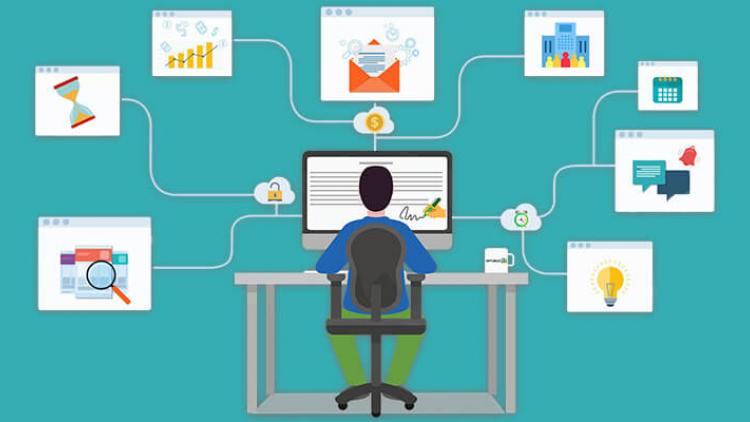
I like to think I'm both results oriented AND process oriented. Quite frankly, I don't really understand why there is so much written about people who are either one or the other. It just seems to me that being results oriented requires solid processes to pave the way toward positive outcomes.
In the cabinet-fixtures-furniture-manufacturing business, I believe that the results - the end product - are the result of having solid, repeatable, documented and extensible workflows. In my humble opinion, my process for drawing a job - my job workflow must be solid, repeatable and documented so that my workflow is demonstrable to whomever needs to know and that I have the necessary "muscle memory" to repeat that process on the next job...and the next after that. And that could be a client or a new employee or the sales team, to name a few examples. Maybe "extensible" isn't exactly the right word. But what I mean by "extensible" is that I believe my workflow must be flexible enough to be adaptable to ANY job and flexible enough so it can grow and change with my project environment and change with my work environment.
The rest of this blog post documents my drawings workflow. These are the steps I take to create a set of shop drawing submittals at Craftsman Engineering.
Resources required at the start of a drawing project.
Before I get started, I like to get my "ducks lined up". Here's a list of things I like to have BEFORE I start drawing and engineering a new job in Cabinet Vision.
- Full Architectural plan set in PDF format. And if that's not possible, I like to have at a very minimum the pages that relate to the scope of work that I will be working with on the project.
But the FULL set is handy to answer questions about HVAC, plumbing etc. as they relate to the casework on this project.
- Notes from the project manager or sales person. These notes and scribbles are valuable in that there is a wealth of "informal" information shared on notes and scribblings from phone conversations and meetings that would not otherwise show up in other "formal" job related documents. These might also include "inspiration photos" or similar sketches from the client to convey the desired "look & feel" of the project.
- Site measurement documents & photos. There's nothing like a photo to relay the real story. In my opinion, photos of every room and wall should accompany all site measurement documentation. It's my experience that nearly every shop and every person who is actually measuring the job, has their own "code" for recording their measurements onto a piece of note paper or onto a copy of the architectural plan set. Knowing that, I like to sit down with the "measuring guy" so that I can understand their "style" of recording measurements so that I can accurately transfer their notes and scribbles to Cabinet Vision.
- Specifications: What are the materials on this project? How about finishes, doors & drawers ( maker, profiles, species )? And countertops ( materials, thickness, edge profiles )? Do we have moldings selections ( profiles, species, size )? We can't forget hoods and other add-ones like Rev-a-Shelf and Hafele products. Are there any architectural plant-ons or turnings etc.? The more detail you can get with specifications, the better. Make, model, SKU etc. is much better than "a garbage pullout"...we need details!
- Appliance schedules: A complete list of appliances including make and model numbers. If possible, get a copy of the invoice from the appliance dealer.
Engineering and Drawing
- Identify all pages in the architectural plan set that are pertinent to the casework/cabinet/millwork sections of this project.
- Print all pertinent architectural pages on tabloid paper. With yellow, blue and orange highlighters, highlight every piece of casework in the project and match to the scope of work documents. Add to hanging file set ( I keep printed material in hanging folders )
- Download all appliance spec sheets including appliance panel sizing specs. Rename pdf spec sheets to match shop drawing naming conventions. Place files in job folder. Update appliance schedule spreadsheet to reference naming conventions.
- If door style, drawer front style, end panel style is not in Door.ddb, add them to the door catalog now.
- If molding style/profile is not in molding library ( crown, base, whatever...) add them to the molding library now.
- If counter top style/profile is not in counter top schedules, add it - regardless of who manufacture the tops. Counter tops will be included on drawings.
- If materials ( panel stock, board stock, drawer guides, pulls, rev-a-shelf items, etc. ) aren't in a materials schedule, add them.
- Determine construction methods ( and their names ) to be used on this project and where they will be applied ( if multiple construction methods )
- Determine which material schedules ( and their names ) to be used and where they will be applied. If new material schedules are needed, create them now.
- Gather any special instructions about the project from the project manager - ex. phasing of the project, schedule constraints, related trades constraints, and which version/build of Cabinet Vision etc. Request farmhouse sink to be delivered to shop by this date _______
- Open Cabinet Vision and start a new project. Give each room a unique and meaningful name - usually matches names and room numbers from the architectural plan set.
- Layout perimeter walls, windows, wall openings, and doors.
- Add temporary CAD layout lines to help locate peninsula walls for islands and peninsulas.
- Add any constrained objects first to the room. Use temporary CAD layout lines, if necessary to help locate constraining objects ( ex. sink center lines, window center lines, appliances, corner cabinets ).
- Add tall cabinets, bases, uppers, and fillers to perimeter and islands. If final measurements aren't yet available, "scale to fit" cabinets per architectural plan set.
- Section each cabinet per architectural elevations.
- Add special objects such as floating shelves, hoods, and architectural posts and plant-ons.
- Add moldings and molding sets including base board moldings and crown moldings ( fluting also, if applicable )
- Auto build counter tops and then shape tops as necessary.
- Repeat 12-19 for each room in the project.
- Go to Drawings tab and make a cover page for this project. Fill in or correct any mis-information. Ensure that paper size is set to 11 X 17 and the default title block is set for this client.
- Create another page. Use table of contents title block for this page
- Create a third page using the blank page ( aka "Boiler Plate" ) title block. If this is a multi-room project, import a dxf or jpg ( screen grab from the architectural plan set ) of the floor plan of this project. Draw blue-line boxes around each room that is included in the scope of work in this project and label each room exactly as indicated on the architectural plan set ( Kitchen, Powder, Laundry etc ). If this project has multiple floors, create a new page for each floor.
- Create drawing scenes for each room. Plan, elevations and sections as necessary.
- Create simple Photovision renderings of views of rooms with unusual or complex features. Send renderings to drawings.
- Add scenes to drawing pages grouped by plan, elevation and section. Arrange and align scenes on each page with the plan in upper left, elevation below the plan and sections to the right of the elevation. If a minimum 1/2" = 1' scale won't allow all scenes to be grouped together on a single page, layout the plan view on a page by itself followed by elevations and sections on subsequent pages.
- Add scene labels to each scene such that the scale is indicated for the scene and page number and unique scene name and code. Symbols should use autotext as much as possible ( ex. Plan 1/9, Section A/10 ) Plans and elevations should be coded as numbers where sections should be
alphabetic - Add scene labels to plan view scenes that "point to" and reference elevations and/or section scenes on this page or subsequent pages. Edit the pointer symbols so they have the correct scene name and page reference.
- Add red section line symbols to elevations where unique sections require a unique section scene.
- Trim/delete any unnecessary dimension lines or unwanted lines from scenes.
- Add "Text Leader" notes to indicate ANYTHING that might be questionable. Be very liberal with Text Leader notes. Indicate type and thickness of counter tops, under cabinet lighting panels, other "hidden" or less-than-obvious features.
- CAD in as-built features with bold green lines...vents, pipes, structures etc. And label the feature.
- Indicate with Text Leaders any work that is to be performed by others ex. Cantilevered top support by others.
- If multiple door and drawer styles are used, use "Door Capsule" symbols that reference the door style. Place the door capsules below every section of doors on bases, above every section of uppers, and to the right or left of every drawer section. The door schedule page toward the back of the drawing package should have text references and images references for every door style used on this job.
- Make a best effort to include any dimensions to indicate where, what size and what shape of any cutting that will involve other trades. Also indicate, if possible, what trade will make the cut. Include an "Initials" comment with the dimensions. This will be used for the tradesman to initial to indicate that he understands that this cut is NOT up to his discretion as to placement or size and relieves us of the "ownership" of that cut.
- Repeat 26-35 for each room in the project.
- Add material schedule pages as necessary for this project.
- Go to page 2 of the drawings and finalize the Table of Contents with new pages, page numbers and descriptions of pages.
- Print all the drawing pages to a PDF. Ensure that the paper size is set to Tabloid ( 11 X 17 ), landscape mode.
- Email PDF file to client. Include time on project report as required
These steps are likely to vary with each job. My process is pretty fluid and it has to be because every job is different. Most jobs won't have ALL the resources needed to start and I have to be flexible enough to accommodate missing and changing information.
Share this with your engineering team. And share your process with me! Between the two of us, we both might "up our Cabinet Vision games".
Add new comment