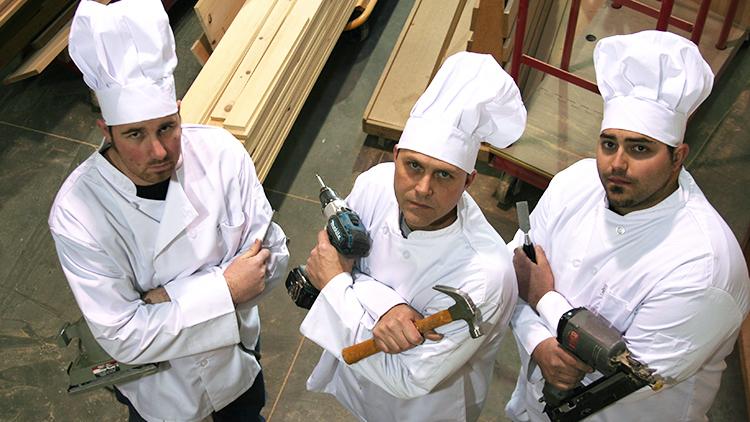
The only thing worse than not knowing what you don't know is not wanting to know what you don't know!
As someone who trains people how to use Cabinet Vision in their businesses, I'm privileged to see the proverbial "lights go on" when clients pick up on and understand the value of a new concept - new to them - in Cabinet Vision.
And I use that word "privileged" because seeing those lights go on tells me exactly where the boundary line is between before Cabinet Vision training and after Cabinet Vision training...especially with respect to the concept or concepts we just covered. For a Cabinet Vision trainer like myself that's great feedback for me and it's a very satisfying thing to witness. It helps me understand my "audience" better and it helps me understand their thinking...their logic...as they worked with Cabinet Vision up to that point. Consequently, I can make mental notes of that moment and apply that to other clients.
It's been my observation that many Cabinet Vision users work without the benefit of the full scope of Cabinet Vision's potential. Some consciously make the choice not to use certain features while others might not use certain features because they've never learned how to use those features effectively...they're "in the dark" about how certain features and basic tools of Cabinet Vision can benefit them.
Work arounds turn into bad habits and bad habits turn into "That's the way we've always done it"
In this example of another mythical shop, this is an established, larger shop - with CNC equipment - and I suspect that they might not be using Material Schedules effectively. Material Schedules aren't really what I'd call a feature but more of part of the framework of Cabinet Vision. At any rate and for the sake of this story, let's say this mythical shop only uses one assembly Material Schedule. It's called "Birch/Birch". That particular schedule is probably familiar to most of us since it comes packaged with Cabinet Vision out of the box. Without going into how or why or who of this particular example, I just want to say that I've seen situations like this repeated over and over again in real life with real cabinet shops large and small.
Before I go on, I just want to say there is absolutely no shame in this. In fact, if this example hits close to home, I applaud you for creatively coming up with work-around solutions in your shop. You've made it this far. But I'm here to tell you, if you can relate to this mythical shop in this mythical example in any way, there are better ways and better days ahead.
Since we're talking about Material Schedules, let's talk about Material Schedules. The whole notion of Material Schedules is kind of abstract. To us old timers who learned how to make cabinets in the 20th century, there were no material schedules. We didn't think in those terms. We thought in terms of measuring and cut lists and sanding and installing and finishing. And I'm using this example for a reason. You see, many people who come from the 20th century may not fully understand the need for such abstract things as Material Schedules or Rate Tables or Profiles or Section Editors or Parametrics or a zillion other abstract terms. And, then these old timers try to move forward with cabinet software without a full grasp of some of the fundamental concepts of how cabinet software works.
Think of a Material Schedule like a List of Ingredients for a group of dinner recipes. We have three recipes...a Greek salad, some Tzatziki and some Lemon Chicken Souvlaki. Every time you make this dinner, you always use the same ingredients. Some of the ingredients are used in more than one recipe and some ingredients are used only in one recipe. The point is that every time you make this dinner, you always use the same set of ingredients. This set of ingredients is in effect a Material Schedule.
Just to make this example a little more playful and meaningful, let's give our list of ingredients a name. Let's call it "Greek Night". Having named our List of Ingredients, it becomes meaningful to me and to whomever will be helping out with meal planning and preparation.
In Cabinet Vision, a Material Schedule is a list of ingredients too. It's a very specific list of ingredients. With a Material Schedule, you tell Cabinet Vision what specific material to use for virtually every single piece of any object you make in Cabinet Vision. And by "object", I mean any cabinet, any fixture, any piece of furniture, counter top, molding etc....anything you design in Cabinet Vision.
For example, if you always use 3/4 Balsa Plywood for your Finished Ends and you always use 1/4" Poplar plywood for your Unfinished Backs, a Material Schedule is where, in Cabinet Vision, that you give Cabinet Vision that information. To make this Material Schedule useful to us and easy to find, we'll give it a unique name. Let's call this one "Lightweight". Now, whenever you want to design something with this set of materials, you can simply use the Material Schedule called "Lightweight".
If you've worked with me before, you've probably heard me say this about Material Schedules, "Material Schedules answer the question 'What do you make your cabinets out of?' while Construction Methods answer the question 'How do you make your cabinets?'"
I'll talk more about Construction Methods in future blog posts. But if you'd like to learn more about how to "up your Cabinet Vision game" before then, reach out to us here at Craftsman Engineering.
Until then, Opa! Opa!
Comments
Cabinet vision Application Engineer
This blog helped me so much. And will be waiting for next blog. Explained neatly with good and simple example, so that everyone can understand simple and easy.
Optimization help
Seeing if you may be able to assist us setting up panel optimization through cabinet vision in the way most productive to our cabinet shop. Checking on consultation cost and time line. Thank you
Add new comment